Home

Our Founder
James Paterson
James was formerly Chief Audit Executive for AstraZeneca PLC from 2002 - 2009. He has worked in a range of other corporate and commercial finance roles, including Head of Group Financial Reporting and Director of Global Leadership Development programmes.
He has been a consultant, trainer and business coach since 2010.
After working on a Masters Degree In Management - he was seconded into HR to be head of Global Leadership Development programmes for several years.
Root Cause Analysis & Culture
Getting to the underlying reasons why things can go off track and understanding the behavioural, 'human factors' that are involved.
Governance & Risk Assurance
Focusing on both accountabilities and how to ensure certainty to within defined tolerances.
Leadership & Political Savvy (Coaching)
Developing an authentic style that is able to identify and adapt to political realities.
Internal Audit
Ranging from internal audit team effectiveness to more tangible good practices including lean auditing.
Other/Miscellaneous
A range of support and training options are available to Audit Committees and teams working in Governance, Risk and Compliance, and Risk Assurance/Control.
Beyond the Five Whys: Root Cause Analysis & Systems Thinking
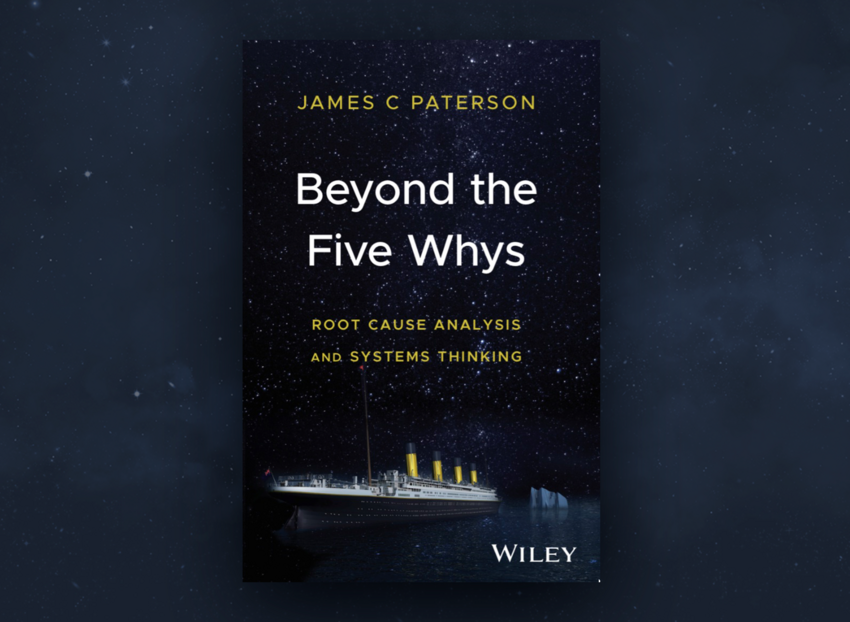
What our readers say...
James Paterson, a former Chief Audit Executive, tackles a topic of immense importance across all organizational sectors. The book also includes practical guidance from leaders in business, risk and audit.
Nancy Haig, CIA, CBA, CFE, CRISC, Principal – PIAC LLC
As the world becomes ever more complex and fast paced it is imperative that we become outstanding at learning from experience. Somehow, we must get beyond blame and shame when examining why things go wrong. Otherwise, we will just repeat, and probably make bigger mistakes.
Andrew Pal, CEng, FIMechE, Leadership Coach and Organisation Consultant
Through clear explanations and real-world examples, readers will learn how to systematically identify root causes and develop effective solutions that address the underlying problems. This book is a valuable resource that professionals can read and start to apply to improve their problem-solving skills and make a positive impact within their…
Sandeep Das, Head of Internal Audit, St John Ambulance
James uses a combination of real-life stories and best practice insight to present a practical approach to root cause analysis that will help shift your mindset to unleash the power of being more curious.
Damian Finio, CFO Phibro Animal Healthcare Corporation
Lean Auditing: Driving Added Value & Efficiency in Internal Audit
What our readers say...
James’ coaching style really works for me, helping me get to the core of the matter and always coming away with my own strategy and next steps. I feel listened to and supported yet challenged, this balance is perfect for moving forward and taking action.
Anonymous
I effectively learned a lot. James was able to explain the complexity and tried to make it simple. Nice balance of theory and practice. I liked the easy going atmosphere. James is one of my favored instructors. He is always very approachable and encouraging. He knows exactly how to trigger you…
Private
The course was very good and informative with James excellent presenter and training and using his wide range of experience and knowledge help illustrate the content.
Private
Thank you again for your participation in the conference. The feedback both onsite and through the speaker evaluation was extremely positive. Attendees found great value in attending your session and even quoted it as the best session of the entire conference! Many requested an encore performance and the opportunity to participate in…
Sheena Majette, The Institute of Internal Auditors
Very good feedback (for you) since 93% was in the 5 (Excellent) or 4 (Very Good) category.
Helena Abel, ACCA UK
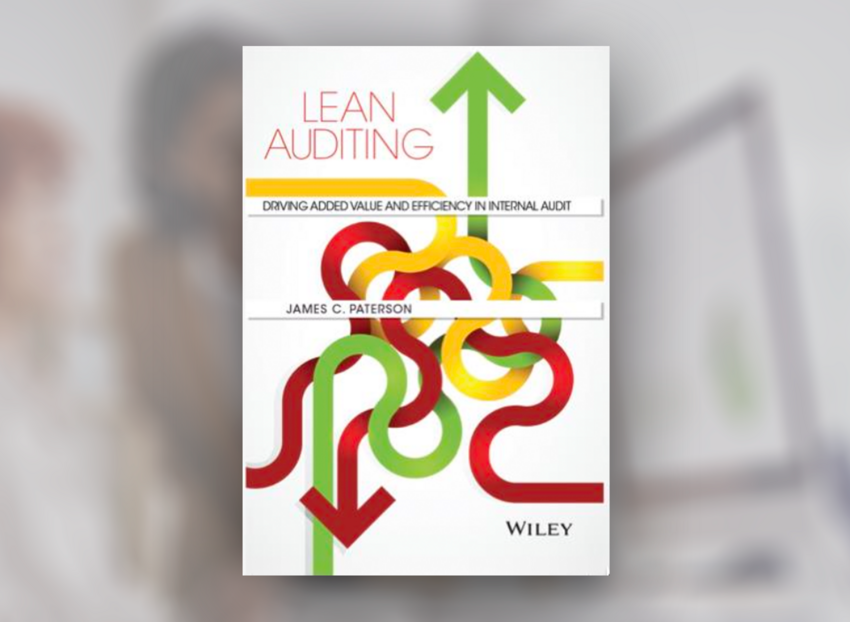